Liquid cooling technology is a cooling technology
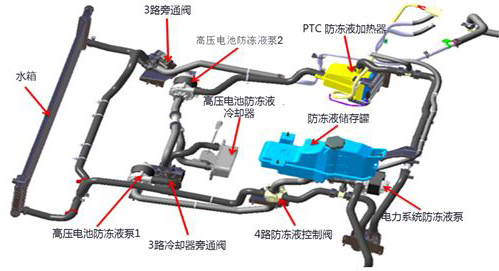
that utilizes the flow of liquids to quickly take heat away. Liquid cooling applications deal with liquid cooling plates (also called water cooling plate) that are installed onto heat sources. It works together with heat exchangers and pumps to dissipate heat by the circulation of liquid. Under typical conditions, liquid cooling applications are used in an environment with higher thermal energy density that either forced convective cooling or phase change system are not able to meet the required cooling effect.
Winshare Thermal keeps investing on the development of liquid cooling technology. We especially focus on renovating the product techniques for water-cooling products and have acquired several technical patents on the techniques including automatic bending of copper tubes, extrusion dies, pressed tubes, bonding and welding, etc. This allows us to produce more reliable cold plates by welding, greatly reduce the failures such as leaks on the cold plates, and enhance the reliability of the cooling capacity of cold plates. With further processing on the surface of liquid cold plates, we can realize better contact with the heat sources and enhance the cooling efficiency.
Water-cooling passages formed by buried tubes + Tube fittings
Water-cooling passages formed by extruded materials + Welding
Water-cooling passages formed by machining + Welding
Water-cooling passages formed by die-casting + Welding
Drawings provided by SVG customer and descriptions of requirements:
Technical descriptions:
(1) Target cooling capacity of the water-cooling heat sink is 920w×2=1840w;
(2) Pressure≤7bar/30min, without any leak;
(3) Ambient temperature during usage: -45℃~45℃;
(4) Cold plate flow resistance: <50KPa, 11L/min, volumetric density: 50% water +50%ethylene glycol solution;
(5) Inlet temperature is 60℃, maximum surface temperature is smaller than90℃ with a temperature difference of 3℃.
Schematic of simulation design model of SVG water cooling heat sink and relevant parameters:
Cooling design parameters:
Water cooling approach, the material is AL6063-T6, cold plate flow resistance:<50KPa, 11L/min; Volumetric density: 50% water +50%ethylene glycol solution; inlet temperature is 60℃. There is no interface between the cold plate and the IGBT.
Schematic of simulation results of cross-sectional temperature loss in the cold plate:
Inlet temperature is 60℃;
Outlet temperature is 63.84 ℃;
Volumetric flow rate: 11L/min。
Schematic of simulation results of cross-sectional speed in the cold plate:
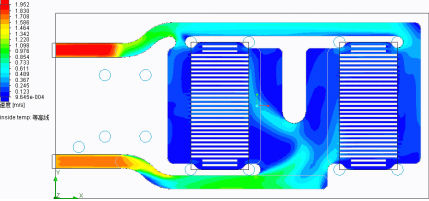
Schematic of simulation results of cross-sectional flow projector in the cold plate:
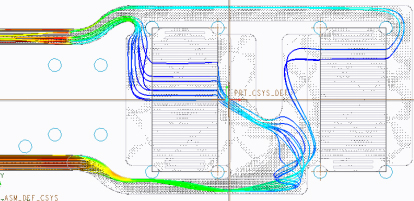
Schematic of simulation results of cross-sectional pressure variations in the cold plate:
Inlet pressure: 102727.78Pa;
Outlet pressure: 101325.02Pa;
Pressure drop: 1402.76Pa.
Schematic of simulation results of IGBT cold plate case temperature variations:
Maximum temperature:85.25℃;
Cold plate temperature difference:83.22℃-82.39℃=0.83℃,
This is smaller than the requirement of 3℃ and this meets the design requirement.
Summary of cooling simulation data:
Cooling solution
|
50% water +50% ethylene glycol
|
IGBT Central temperature ℃
|
Max temperature on the cold plate
|
Volumetric flow rate
|
Inlet temperature
|
Pressure drop
|
#1
|
#2
|
Temperature difference
|
Cold plate
|
85.25℃
|
11L/min
|
60℃
|
1402.8Pa
|
82.39
|
83.22
|
0.83
|
Couplers for selection in the water cooling solution:
Pipework for selection in the water cooling solution:
Bellows
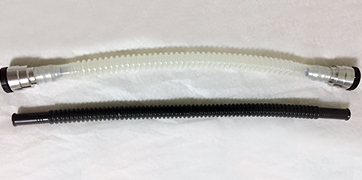
Straight tube
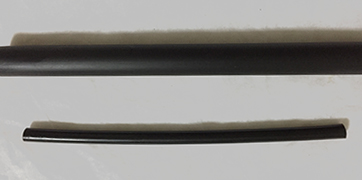
Forming tube
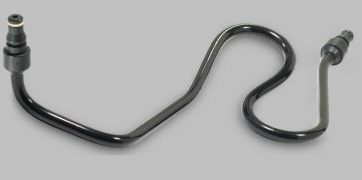