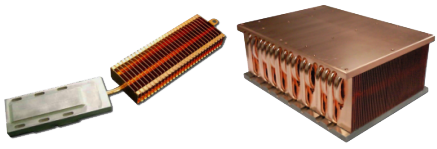
Heat pipe is a heat-conducting component which has very high thermal conductive performance. It was developed by the Los Alamos National Laboratory in 1964 and reached the research climax in the 1960s and began a large number of applications in the industry. It can transfer heat in a completely sealed vacuum tube via the phase change of the working fluid between vapor and liquid states. It has very high thermal conductivity and is more than 100 times higher than the thermal conductivity of pure copper and therefore it earned the reputation of “thermal superconductor”.
Heat pipe heat sinks are new products which are created by utilizing the heat pipe technology to achieve major improvement on old-style heat sinks or heat exchanging products and systems.
Since the invention of heat pipes, there have been new developments on the cooling systems of electronics. Whatever approach we use for cooling, the ultimate cooling medium is air and all of the other media are simply intermediate. The free convection cooling of air is the most direct and simple approach. Heat pipes are capable of quickly increasing the application area of self cooling. Since a heat pipe self-cooling system does not need any fan, it generates no noise and it doesn’t require maintenance so it’s safe and reliable. Heat pipe air cooling or self cooling can even replace water cooling systems so as to reserve water resources and the investment on relevant auxiliary equipment. Moreover, the heat pipe cooling approach allows the heat-dissipating devices to be concentrated and even sealed. This allows the cooling parts to be relocated to the exterior or in the distance so as to enhance the safety, reliability, and application range of electronic equipment and realize the dust-proof, damp-proof, and explosion-proof requirements.
Heat pipe heat sinks in the power electronics field can be classified as follows according to the techniques used.