In our earlier article, the editors introduced our readers to the types of LED heat sinks. Among those types, highly conductive thermoplastic heat sink is also one of them. This type of heat sinks has been valued by people in recent years due to the technical development of the highly conductive materials and the reduction of costs.
The development of cooling technologies cannot sustain without the development of cooling materials. Recent developments of highly conductive thermoplastic heat sinks are gaining speed. This type of heat sinks is made entirely of plastics but its thermal conductivity is more than ten times higher than typical plastics to the range of 2~9 W/m-K. It has excellent thermal conductivity and thermal radiation capabilities. It can be used on light fixtures of various power ranges as a new type of cooling material with insulation capability and can be widely used on LED light fixtures of 1W~200W.
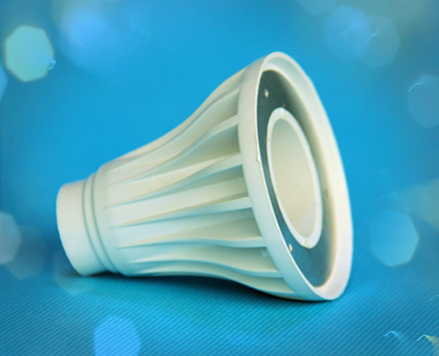
Besides, the dielectric strength of highly conductive thermoplastics is also very good. The dielectric strength level of it can reach 6000V, which is suitable for non-isolation constant current power supplies and high voltage linearconstant current power supplies of HVLED. It allows this type of LED light fixtures to better pass strict safety certification of CE, TUV, and UL.HVLEDs typically operate at high voltage (VF=35~280VDC) and small current (IF=20~60mA) and therefore the heat dissipation of HVLED mainboard can be reduced. Highly conductive thermoplastic heat sinks can be formed by conventional injection molding machines or plastic extruding machines. It requires only one-step forming and the surface finish of the final product is high. It can greatly enhance production efficiency and allows high flexibility in styling designs so as to bring a designer's design concept into full play.。
For the eco-friendly consideration, highly conductive thermoplastics heat sinks are aggregated from PLA (corn starch). It can be completely degraded with no residual or chemical pollution. The production process meets the worldwide environmental requirements without any heavy metal pollution, no exhaust water, and no exhaust gas.
Nano-scale metallic ions are densely filled between the PLA molecules within the highly conductive thermoplastics heat sinks. They move rapidly under high temperature and can increase the thermal radiation energy. Their vitality is superior to heat sinks of metallic materials. Highly conductive thermoplastics heat sinks can resist high temperature and it will not break for five hours under 150℃ and will not deform. When it is used with high voltage linear constant current IC driven solutions, there is no need for electrolysis capacitors or large volume inductance so that the LED service high is greatly extended. For non-isolation power supplies, it results in higher efficiency at a lower cost so that it is especially suitable for applications such as fluorescent tubes and mining lamps.
For the heat sink surface designs, highly conductive thermoplastics heat sinks can be designed with many thin cooling fins and it is always possible to make the cooling fins thinner in a greater number so that the cooling area can be extended to the maximum extent. During operation, the cooling fins automatically result in air convection for the diffusion of heat so that the cooling effect is better. The heat generated on the LED light bulb can be transferred directly to the cooling fins via the highly conductive thermoplastics and can be quickly cooled via air convection and surface radiation.
From the weight aspect, the density of highly conductive thermoplastics heat sinks is smaller than aluminum. The density of aluminum is 2700kg/m3 and that of plastics is only 1420kg/m3 which is just about half of that of aluminum. Therefore, for a heat sink of the same shape, the weight of a plastic heat sink is only half of that of an aluminum one. Moreover, it requires simpler processing and the forming cycle time is 20~50% shorter so that there is room for cost reduction.
Highly conductive thermoplastics heat sinks have advantages for a plurality of aspects and therefore more and more LED heat sinks use this cooling approach in recent years. With further developments in the future, it is possible that highly conductive plastics might replace those heat sinks made of pure metals.