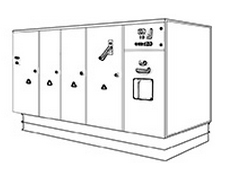
Via the excitation on the rotor of the doubly-fed induction wind generators, wind power converters are capable of making the amplitude, frequency, and the phase of the stator of the doubly-fed generator the same as the electrical grid. Depending on the requirements, it can also carry out the independent decoupling control of active or reactive power. Using converters to control the doubly-fed induction wind power generators can realize the soft cut-in control and reduce the adverse effects of the cut-in impulse current on the electric motor and electrical grid. In other words, whether a wind power converter operates stably will directly affect the stability of the electrical grid. In order to ensure the normal operation of the wind power converters, cooling is an indispensable and critical part.
Simulation model and relevant parameters of the converter:
Ambient temperature is 25℃
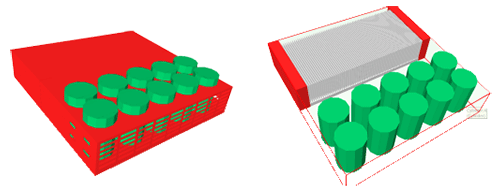
IBGT model and relevant data:
Schematic of the internal structure and heat-dissipating devices of Infineon: diode:34W; IGBT:91W; total 1500W;Assuming the thermal interface material is:thermal grease 7762,thickness=0.2mm, K=4W/m*K。
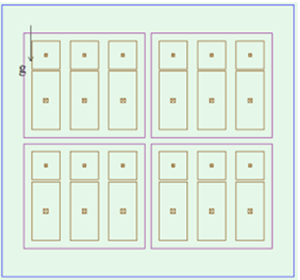
Working state of the heat source:
0-29s:0%;
29s-30s:from 0% to 100%;
30s-59s:100%;
59s-60s:from 100% to 0%;
Cycle time for one operation is 60S.
Simulation model and relevant parameters of the heat sink design:
Heat sink parameters:
Dimensions of base plate:462*220*15mm;
Fin thickness: 1.5mm;
Fin count: 92fins;
Fin height:87mm;
Material:AL 1060;
Machining technique:Skived fin;
The operation ran for 16 cycles with a total time of 960s.
Schematic of the simulation results for the converter:
Schematic of the variable of temperature Tb vs. time:(Airflow:500m^3/H)
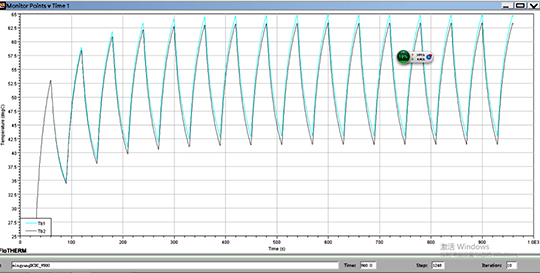
Schematic of the variable of IGBT core component's bottom surface temperature vs. time:
(Airflow:500m^3/H,IGBT node temperature = Core component's surface temperature + Core component's power*Core component Rj-c)
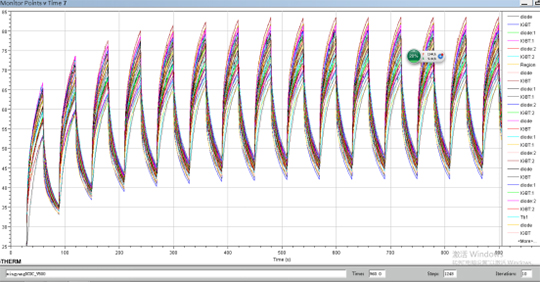
Schematic of the variation of temperatureTb vs. time:(Airflow:600m^3/H)
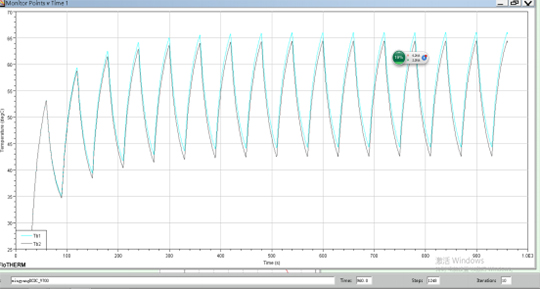
Schematic of the variation of temperatureTb vs. time:(Airflow:700m^3/H)
Schematic of the variation of temperatureTb vs. time:(Airflow:800m^3/H)
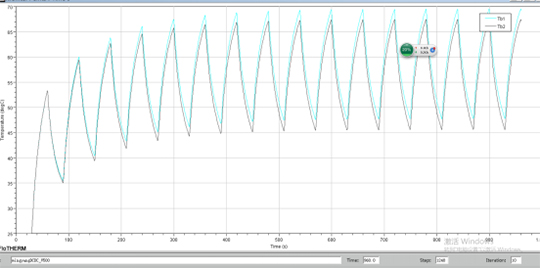
Simulation results of the variation of maximum temperature between the heat source bottom and the heat sink surface vs. time in cycles:
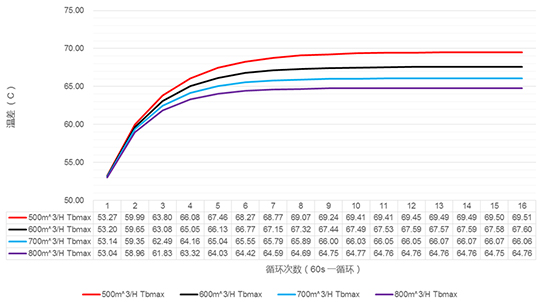
Simulation results of the heat sink's pressure loss vs. flow rate:
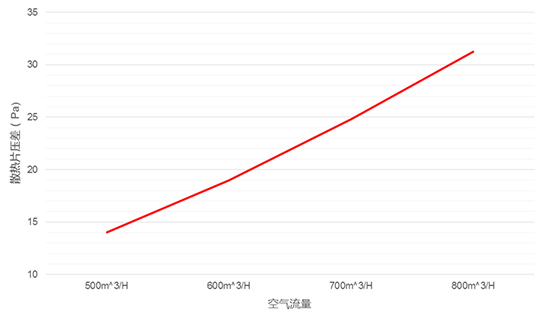