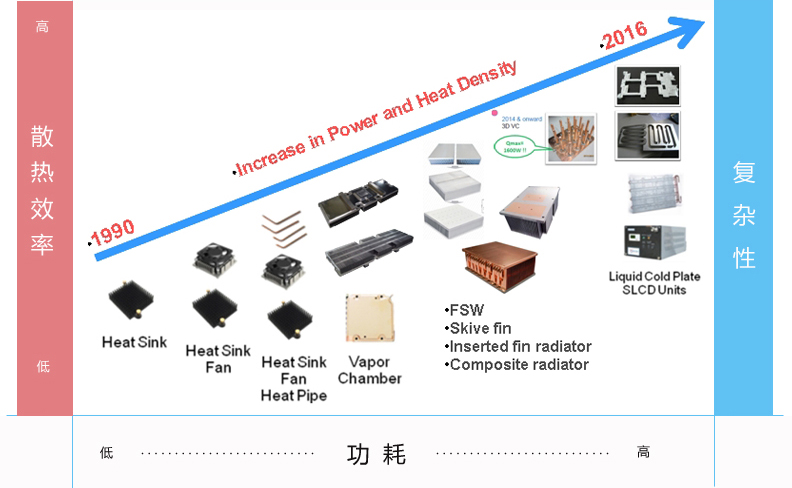
During the period of 1990 to 2016, new product developments in various fields moved toward the direction of concentrated heat sources with higher power and higher density. This trend applied more stringent requirements on the cooling capacity and special limitation on a cooling system. It has been more obvious since 2010 when the density of industrial products increased rapidly with the renovation of high-density cooling technologies and solutions. In the last couple of years, skived fin, heat pipe thermal module, 3D/VC applications, and micro-channel liquid cooling have become the mainstream cooling techniques.
The above figure embodied the distribution of performance and technical difficulty of various types of cooling products along with the individual power dissipation within applications and thermal management. The horizontal axis indicates the total power to be dissipated and the vertical axis indicates the relationship between thermal resistance, total power, unit volume, and heat flux. This tool is for resolving the thermal problem and locating the starting point of a solution. To determine an adequate solution for an application, the default power dissipation can be positioned along the horizontal axis and move along the vertical axis so as to find the corresponding Winshare Thermal's cooling solution. Depending on the total power and the dynamic system configuration, there might be several suitable cooling mechanisms to resolve the thermal problem.
(1) Natural cooling: Natural cooling is a type of cooling approach that is in common use. It utilizes the high thermal conductivity of materials (mostly extruded materials) to carry heat away and dissipate the heat to the ambient air. Even if there is no specific airflow speed requirement, it is still feasible to realize the cooling of a product by using natural cooling heat sinks which are made by copper-aluminum cooling plates, aluminum extruded parts, machined parts or die-casting alloys.
(2) Forced air cooling: Forced air cooling that uses dedicated or system-level fans to realize convection under the conditions with special air flow velocity requirements. A configuration with coolers, high-density fin assemblies, and heat exchangers can generate an environment with counter flows or intercross air flows so as to speed up removing the heat and enhance the cooling efficiency. Force air cooling techniques can also work together with cooling techniques with phase-changing fluid which is typically contained inside a sealed copper heat pipe. The cooling effect is realized by the rapid alternation of liquid evaporation and condensation at a lower boiling point. When a product has a higher density or when the space is confined, the cooling capacity of a heat sink can be enhanced when heat pipes are integrated into the design.
(3) Liquid cooling technology: Liquid cooling applications deal with liquid cooling plates (also called water cooling plate) that are installed onto heat sources. It works together with heat exchangers and pumps to dissipate heat by the circulation of liquid. Under typical conditions, liquid cooling applications are used in an environment with higher thermal energy density that either forced convective cooling or phase change system are not able to meet the required cooling effect. In recent years, Winshare Thermal strengthened our development of liquid-cooling technology and especially the continuous renovations of production techniques for water-cooling products. This allows us to produce more robust cold plates by welding, greatly reduce the failures such as leaks on the cold plates, and enhance the reliability of the cooling capacity of cold plates.
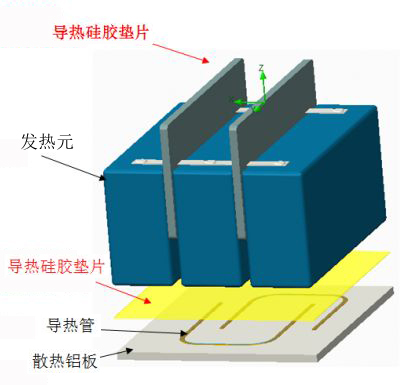
Natural cooling
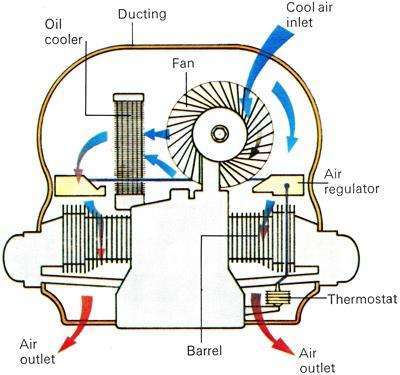
Forced air cooling
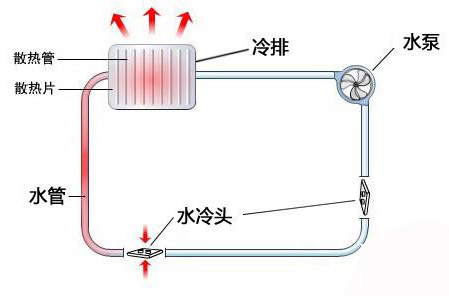
Water/liquid cooling
Winshare Thermal's thermal management engineers have abundant experiences in the project research and development, design, and testing of various fields related to networks, telecommunication, consumer electronics, power energy transformation, new energy cars, and biomedical equipment.
We are capable of several tasks as follows:
Carrying out simulation and analyses of thermal conduction, convection, and radiation
Optimizing ventilation and the configuration of fans
Enhancing power density
Reducing noise, cost, and volume
Improving MTBG (Mean Time Between Failures)
Our professional thermal management engineers can provide the most advanced and most efficient cooling solutions under the consummate customization process and system. We can save unnecessary costs on the design resources, thermal modeling, and testing equipment. From a design concept to its production, Winshare Thermal's R&D department can always provide you with cooling technical support at any moment.